自動旋盤による穴あけ加工とは?
自動旋盤加工工程の一つである穴あけ加工は、工業製品の製造において非常に重要な役割を果たす加工方法です。穴あけ加工はさまざまな業界や製品において幅広く使用されており、例えば、自動車産業ではエンジンのシリンダーブロックに穴をあけるために使用されたり、電子機器の製造では基板に穴を開けるために使用されます。また、建築業界では配管や取り付け穴を作るために穴あけ加工は欠かせません。
ここでは自動旋盤加工の基本となる穴あけ加工について述べていきたいと思います。
自動旋盤によるドリル穴あけ加工
ドリル加工とは、固定した加工物に回転する工具をあてることで穴をあける加工方法です。自動旋盤加工では回転させた材料に固定した工具をあて穴をあける加工方法が一般的です。用途に合わせての大小様々な穴を空けることが可能です。
回転した被削材に固定した刃の部分が接触することで削り取り、切りくずを排出しながら穴を掘り進めることができる切削工具です。 多種多様な種類の中から製品を選ぶことで、さまざまな場面で活躍します。
自動旋盤によるタップの下穴加工の役割
タップの下穴加工には以下の通り重要な役割があります。
1.正確なねじ切り:下穴が正確に位置していない場合、ねじが歪んだり、ねじ山が不均等になったりする可能性があります。下穴を適切に加工することで、ねじが正確かつ均一に切れるようになります。
2.穴の位置と深さの制御:下穴加工を正確に行なう事で、ねじが正確に配置され、必要な深さまでねじが入るようになります。これにより、部品や機械の正確な組み立てが可能になります。
3.ねじの強度と安定性: 下穴加工は、ねじの強度と安定性にも影響を与えます。正確に下穴を加工することで、ねじの根元部分がしっかりと材料に嵌り込むため、ねじがより強固に固定されます。これによりねじが緩むことなく正確な位置に留まり、材料や構造物の安定性が向上します。
4.ねじの寿命と耐久性: 精密な下穴加工によってねじが正確に配置され、適切な深さで切られると、ねじの寿命と耐久性が向上します。正確な下穴により、ねじへの負荷が均等にかかり、ねじが適切に支持されるため、ねじの疲労や断裂のリスクが減ります。
このようにタップの下穴加工は、ねじの正確な切り込み位置や深さ、強度、安定性、耐久性を確保するために欠かせない工程です。正確な下穴加工を行うことで、安全性や品質の向上、そして効率的な組み立てプロセスを実現することができます。
リーマ、ボーリング加工の下穴加工の役割
仕上げ穴加工の穴精度は下穴精度によって決まると言っても過言ではありません。リーマは、穴の精度や表面仕上げを向上させるための切削工具で、自動旋盤による穴あけ加工では、リーマを使用して穴を精密に仕上げることができます。リーマ穴によって、穴の寸法や円形度、表面の粗さを改善し、部品の正確な組み合わせや運動のスムーズさを確保することができますが、その精度を安定させるためには下穴加工の精度が重要になってきます。
また、下穴加工の済んだ穴を広げ精密な穴加工が可能なボーリング加工においても下穴加工の精度は重要になってきます。穴サイズや形状など、ボーリング工程で均等な負荷となるよう精度が求められます。均等な負荷により加工面が滑らかで均一な仕上げとなることで、部品の動きや材料の摩擦を改善し、部品の寿命や耐久性を向上させることができます。
自動旋盤を用いた穴あけ加工品
ここからは、自動旋盤を用いて穴あけ加工を行った、当社の事例を紹介します。
液晶フィルム切断部品用ピン

こちらは、液晶フィルム切断部品用ピンの加工事例となります。
材質は、S45Cで、旋盤加工、ミーリング加工、クロス穴加工により製作を行ないました。こちらの製品の加工におけるポイントは、旋盤で加工をおこなうことでコストメリットを生み出している点と、クロス穴に高精度なザグリを入れている点です。 こちらの製品の形状は、通常であれば、マシニングセンタで加工を行なうことが多い形状ですが、こちらの事例では、旋盤加工で製作しています。マシニングセンタでは、2工程から3工程必要になるところを、旋盤であれば1工程で済むため、コストメリットがあります。こちらの事例では、月産5000個で生産しました。 また、高精度なクロス穴のザグリを、刃具の選定、加工のノウハウにより実現しており、精度は以下のようになっております。 ねじ部軸精度:30μ 面粗度:Ra1.6 重なり合う二つの穴のはめあい公差:H7 真空超音波洗浄も施しており、表面の微細なごみも除去しています。
エンジン出力調整用スロットルブッシュ
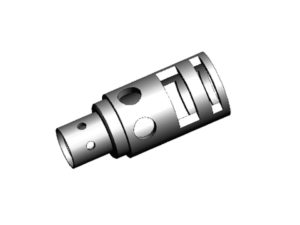
こちらは、エンジン出力調整用スロットルブッシュの加工事例です。
材質は、SUM23で、旋盤加工、クロス穴加工により製作を行ないました。こちらの製品における加工のポイントは、クロス穴のバリを除去している点と、肉薄形状の加工を行なっている点です。 こちらの製品には、多数のクロス穴がありますが、刃具の選定、治具の調整によりそれらクロス穴のバリ除去に対応しております。また、肉薄形状のため変形がしやすいところ、工程組を工夫することによって、以下の精度を満足しています。 外径公差:9μ以内 内径公差:18μ以内 面粗度:Ra1.6 こちらの製品には、真空超音波洗浄も施しており、表面の微細なごみも除去しています。
産業機器用ノズル
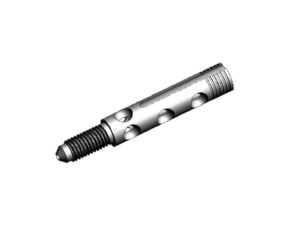
こちらは、産業機器用ノズルの加工事例になります。
材質はSUS303で、旋盤加工に加え、内径ねじ加工、外径ねじ加工、クロス穴加工を施し、製作を行ないました。 こちらの製品の加工におけるポイントは、 内径段付き加工を高精度に行なっている点と、軸部のテーパー形状の管理寸法±2μ以内を実現している点です。 内径の段となっている部分は、断熱材噴出ノズルの核となる部分で、噴霧量を変化させるための角度、公差が非常に厳しいです。 加工順を工夫することで、高精度な加工を実現しました。
ここ文章が入る。
ケーブルホルダー
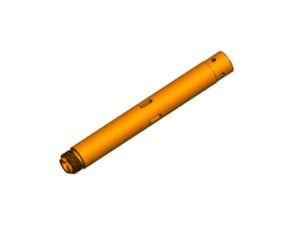
こちらは、電機製造用のケーブルホルダーになります。
材質はC1100で、旋盤加工、ドリル加工、ミーリング加工により製作しております。 こちらの製品における加工におけるポイントは、タフピッチ銅で要求された精度を満足している点です。タフピッチ銅は、粘りがあり、バリが出やすいため、加工しにくい材質ですが、当社でのノウハウを活かし、適正な切削条件で加工を行なうことにより、以下の精度を実現しています。 外径公差:50μm以内 アスペクト比:約16.6 面粗度:Ra1.6以下 同軸度:50μm こちらの製品では、同軸度は50μmですが、自動旋盤加工コストダウンセンター.comでは、同等の長さであれば、同軸度30μmまで出すことが可能です。
カテーテルチップ
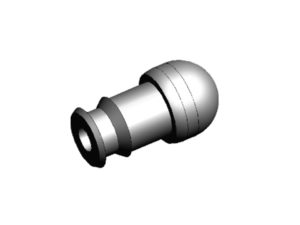
こちらは、医療現場で用いられるカテーテルの先端部品の加工事例になります。
材質はSUS316で、旋盤加工とドリル加工により製作しました。 こちらの製品における加工のポイントは、バリが出ないように加工を行なっている点です。 SUS316はSUS304より加工変形が多いため、適正な刃具の選定し、エッジ部のバリの除去、精度穴加工を行なっております。医療で用いられるため、バリがあってはならず、バリが出ないように加工を行ないました。 また、切削条件を最適化することで、以下の精度を実現しております。 寸法公差:20μ以内 同芯度:10μ以下 Rs:3.2以下 また、こちらの製品には、真空超音波洗浄を施しており、表面の微細なごみも除去しております。
自動旋盤による穴あけ加工のことなら当社にお任せください
フジタイトではNC自動複合旋盤に特化しており、様々な素材の切削加工を行っております。また刃物を自社で制作しており、製品ごとに最適な加工を行うことができるため、ステンレス、チタンなどの難削材にも対応しております。
また、VA・VE提案も行っておりますので、ご気軽にご相談ください。旋盤による切削加工は是非当社にお任せください!