製品を製作する上で、費用は特に重要な要素です。
費用を下げることは会社の利益率アップに直接的に繋がります。
しかし、費用を抑える、コストダウンすることは、容易ではありません。
安易にコストダウンをしようとすると、製品の品質低下に繋がりかねません。
そのため、コストダウンを実現するためには、
・どの工程で、どのような費用が発生するか
・どの工程で、無駄が発生しているか
・無駄のある工程を、どのように改善するか
を知る必要があります。
今回は、切削加工における以上の3つのことを、当社のコストダウン事例をまじえて、具体的に解説します!
切削加工にかかる費用の構成要素
切削加工における費用を構成する要素は大きく分けて、5つあります。
5つの要素は以下の通りです。
①被削材の材料費
②被削材の硬さ
③被削材の加工費
④切削工具の費用
⑤加工手順の複雑性
これら5つの要素をひとつずつ解説していきます。
被削材の材料費
切削加工における費用の構成要素として、第一に上げられるものは被削材の材料費です。
当然ではありますが、被削材が大きければ大きいほど材料費は高くなります。
また、被削材自体が高価な場合もあります。
代表的な高価な被削材は、チタンとニッケルです。
チタンは軽量で硬度が高いという性質を持っています。
ニッケルは高い耐熱性を持っています。
チタンとニッケルはこのように優秀な性質を持っていますが、非常に高価です。
このような高価な被削材を使用すると、材料費が高くなってしまいます。
被削材の硬さ
被削材の硬さも、切削加工における費用を構成する要素の1つです。
被削材が硬ければ硬いほど、加工に時間がかかります。
加工に時間がかかると、1つの製品の製作にかかる光熱費や人件費、切削油などの消耗品の費用が増えます。
そして、結果的に費用が高くなります。
また、被削材が硬ければ、切削工具の摩耗を激しくなります。
それにより、使用する切削工具の寿命が短くなります。
そうすると、切削工具を買い替えるために費用が多くかかってしまいます。
被削材の加工費
被削材を加工する際も、費用は掛かります。
特に、難易度の高い加工は費用が高くなりやすい傾向にあります。
具体的な例として、面取り加工におけるC面とR面が挙げられます。
C面加工は角を45°に削る加工で、R面加工は角を丸くする加工です。
C面加工に比べ、R面加工は難易度が高いです。
そのため、R面加工は費用も高くなります。
また、切削加工後に追加で他の加工が必要な場合も、必然的に費用が高くなります。
切削工具の費用
切削加工を行なうために必要である切削工具も、費用を構成する要素の内の1つです。
当然ではありますが、切削加工を行なうと切削工具を消費します。
また、切削工具の使用頻度が高ければ、切削工具の消費量は増加し、
また、「被削材の硬さ」の項目でも述べた通り、被削材が硬ければ、使用する切削工具の寿命は短くなります。
このように、切削工具の使用頻度や、被削材の硬度に切削工具の費用は影響されます。
加工手順の複雑性
加工手順が複雑性を増すと、費用が高くなります。
これは、切削加工機を動かす回数が増えるためです。
切削加工機を動かす回数が増えると、切削油や切削工具の消耗が激しくなります。
また、切削加工にかかる時間も増え、1つの製品の製作にかかる光熱費や人件費、切削油などの消耗品の費用が増えます
そのため、加工手順の複雑性が増すと、結果的に費用が高くなります。
切削加工のコストダウンのためにできること
次に切削加工のコストダウンのためにできることを、先ほど説明した費用の構成要素を踏まえて説明します。
被削材の変更
被削材の変更はコストダウンに大きく影響します。
最適な被削材を選定しなければ、切削加工のコストダウンには繋がりません。
最適な被削材を選定する上で重要なポイントは2つあります。
1つ目は被削材の大きさです。
切削加工において、被削材を削る量が多ければ多いほど、費用は高くなります。
また、被削材を削った分だけ、被削材が無駄になってしまいます。
これを踏まえ、コストダウンにするためには、最適な大きさの被削材を選定する必要があります。
被削材が大きすぎるならば、小さな被削材を選定すればコストダウンに繋がります。
また完成品が細長い形状であれば、大きな塊の被削材では無く、棒状の被削材を選定することによりコストダウンに繋がります。
2つ目は被削材の材質です。
切削加工における費用の構成要素でも述べたように、被削材が硬ければ費用の増加に繋がります。
また、チタンやニッケルのような高価な被削材を使っていれば、費用の増加に直接的に繋がります。
これらを踏まえて、コストダウンを実現するためには最適な材質の被削材を選定する必要があります。
例えば、チタンやニッケルのような高価な素材は他の素材では実現できない場合にのみ被削材として使用し、硬すぎる被削材を用いているならば最適な硬さの素材に変更することにより、コストダウンに繋がります。
切削工具および加工手順の最適化
切削工具および加工手順の最適化により、コストダウンを実現することができます。
例えば、段付きの穴を開ける際に2種類のドリルを使っているとします。
このような場合は、段付きドリルを使用することで使用するドリルを1種類のみにすることが可能です。
そうすると、購入する切削工具の本数は1/2に削減でき、加工手順も短縮できます。
加工手順が短縮されると、1つの製品の製作に必要な光熱費や人件費、切削油や切削工具の消耗が抑えられ、コストダウンに繋がります。
このように切削工具および加工手順を最適化することにより、コストダウンを実現が可能です。
当社の切削加工・旋盤加工のコストダウン提案
ここでは、当社の切削加工のコストダウンを実現したコストダウン提案事例をご紹介します。
①面取り加工によるバリ処理加工レスでコストダウン

面取りの指示がない箇所にはバリが発生しやすくなります。そのため、バリ処理工程を踏む必要があり、加工工数が増えてしまいます。 加工工程が増えてしまう分、コストがかかってしまうことが課題でした。
②S45CからS45CFへの材質変更によるコストダウン及び寸法精度安定化
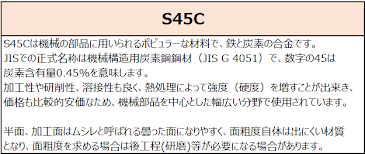
機械構造用炭素鋼のS45Cはポピュラーな材質で、機械部品を設計する時には採用を検討されることが多い材質です。しかし、S45Cはむしれるなど表面が荒れやすい特性があり、切削性は比較的良いものの面粗さを維持するのは難しい材質です。 そのため、面精度を維持しようとすると刃持ちが悪くなってしまうことが課題でした。
③ザグリ加工による高アスペクト比の高精度穴加工のコストダウン
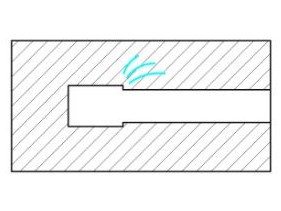
高アスペクト比(穴直径に対し、深い穴)の高精度穴をあける際、底面がフラットの場合は、段階を分けて上から精度を保ちながら加工を行なう必要があります。
高アスペクト比の高精度穴を開けるには細長い刃具が必要になりますが、加工を行なう途中で、細長い刃具の先端部分が、曲がりやすくなってしまうため、精度を保つには、加工工数を増やさなければなりません。また、併せて高い管理能力が必要となります。
切削加工・旋盤加工における、当社のコストダウン能力
自動旋盤加工 コストダウンセンター.comを運営するフジタイトは、充実した設備を保有し、最大60万個/月の旋盤加工品の量産が可能です。また、コストダウン実績を数多く持ち、海外生産と同等価格で旋盤加工品を提供します。
当社が旋盤加工の委託先として選ばれる理由について、以下に詳細を記載していますので、ぜひご確認ください。
旋盤加工のことなら当社にお任せください!
自動旋盤加工 コストダウンセンター.comでは、旋盤加工のコストダウンを得意としています。また、多数の切削加工・旋盤加工におけるコストダウン実績がございます。
また、材質変更や加工工程の低減などによるコストダウンなど、VA/VE提案も多く行なってきました。切削加工のコストダウンでお困りの方はぜひ当社までお問い合わせください。
>>ご相談・お問合せはこちら